Sixty Sixty One: From Aluminum Alloy to Wearables
By creating garments inspired by A6061 — the most commonly used aluminum alloy in the world — MIT students interrogate our relationship to time and nature while demonstrating inspiring skills. Starting from scratch, they imagined, designed, prototyped, iterated, styled, and showcased their work as a team.
By Adelaide Zollinger
May 9, 2024
Sixty Sixty One is a project by MIT undergraduate students exploring aluminum alloy 6061, the most commonly used in the world.
Led by Gloria Zhu, '26, a DesignPlus First-Year Learning Community alumna, the project involved several fabricators, models, stylists, and photographers (all listed below) to create and showcase metal outfits inspired by nature that illustrate the tension between the ephemeral and immortality.
It was featured in the Issue 12 of the Infinite, “a student-run magazine seeking to reframe art, politics, culture, and aesthetics through the lens of fashion.” In the spread dedicated to Sixty Sixty One, the magazine reads: “It is a contemplation of the ephemera of nature, of immortality, of bone and shell and skin, and the forms that stay far beyond our time.”
Sixty Sixty One also made an appearance at the MIT Gala, which took place in the Burton Conner Porter Room on April 28, 2024. The Gala showcased art by independent creators, creations from classes on campus, and a runway where MIT models displayed designers’ work.
TEAM
Spread lead: Gloria Zhu '26
Fabricators: Teresa Jiang '26, Lee Liu '26, Fernando Valenzuela '26, Lindsay Reyes '26
Models: Sabine Chu '26 (also MIT Gala Runway model), Bukunmi Shodipo '24, Anna Chan '26
Styling: Joanna Cao '24 (photoshoots), Sophie Fan '26 (MIT Gala)
Photographer: Michelle Xiang '26 (for photoshoots and MIT gala), Jack Field (MIT Gala)
Answers by Gloria Zhu
Q: WHAT DID YOU MAKE?
A: For Sixty Sixty One, we designed, laser cut, and assembled a variety of metal garments and accessories; these included a corset, purse, skirt, finger cuffs, necklaces, wings, etc. Everything was laser-cut and manufactured in the Morningside Academy for Design N52 space, using parts and tools (bolts / drills / pliers / glue...) from N52 and Metropolis. We also did three photoshoots (one per model) in the N52 photo studio.
Q: WHY DID YOU MAKE IT?
A: I think the mechanical properties of sheet metal really make it stand out as a material for making wearable items. It's structural in a way that allowed us to add a lot of dimension to our pieces just by bending extended lengths of metal, and it just has a really cool texture and sheen. Not to mention we can laser cut and fasten it using joinery like rivets and bolts, which ties in with the mechanical engineering experience of our fabrication team.
Q: HOW DID YOU MAKE IT?
A: Our primary form of fabrication was laser cutting metal using the fablight machine in the N52 MAD fabrication shop, and we also did the brunt of our ideating and prototyping there. Each piece originated as a digital or pencil sketch, which we would then vectorize in Adobe Illustrator and convert to a .dxf file. After cutting the shapes out in the metal, it was then a matter of attaching them to each other — we used a wide variety of fastening techniques, including bolts, rivets, jump rings and chain, clasps, and, if all else failed, zip ties.
Our secondary material after metal was pearls; we had a pack of 5,000 faux pearls, and we probably hand glued hundreds of them onto the pieces over the course of the spread. I'm pretty much an expert at picking up tiny pearls with tweezers now.
Most of the pieces underwent some form of prototyping: maybe a connection point would be too fragile when bent and would snap, or we would need to go back and add clearance in order for two pieces to slot together perfectly. For the wings, top, and skirt, which were larger and needed higher levels of structural integrity, we cut prototypes out of chipboard first to test geometries before cutting into our precious stock metal for the final pieces.
The fabrication was definitely an interesting way of thinking about 3D objects, since the whole process wasn't sheet metal fabrication nor garment sewing in the traditional sense. Instead, it was something in the middle, where if we wanted something to bend around the body in a certain way, we'd have to feel out the limits of the metal and how willing it was to deform in that direction.
Some structures were simply impossible to make out of just one sheet of metal, even if they technically worked in 3D, since, once flattened, parts of the shape would overlap each other in the design. But we could also do a lot of things we couldn't do with textiles, such as adding struts that stick out or bend in a very specific way.
Q: WHAT INSPIRED YOU?
A: I just really like chrome textures and laser cut sculptural shapes so I wanted to try making something cool! Honestly, it was just dope to explore a new material and work with such a great team. For my pieces specifically (the face mask and top), I was inspired by beetles and scarab carapaces, while Lee was inspired by organic and skeletal forms — especially deep sea life — for the skirt and bag.
Q: WHAT ARE YOU GOING TO MAKE NEXT?
A: I can't speak for the rest of the team, but I'm currently working on an interactive installation that will hopefully go up next February! But in the shorter term, I'm having a lot of fun with graphic design at the moment. Working with physical mediums is fun but tiring... for now, I like living in Photoshop land, since I can just sit at my laptop :).
Related News
Related Events
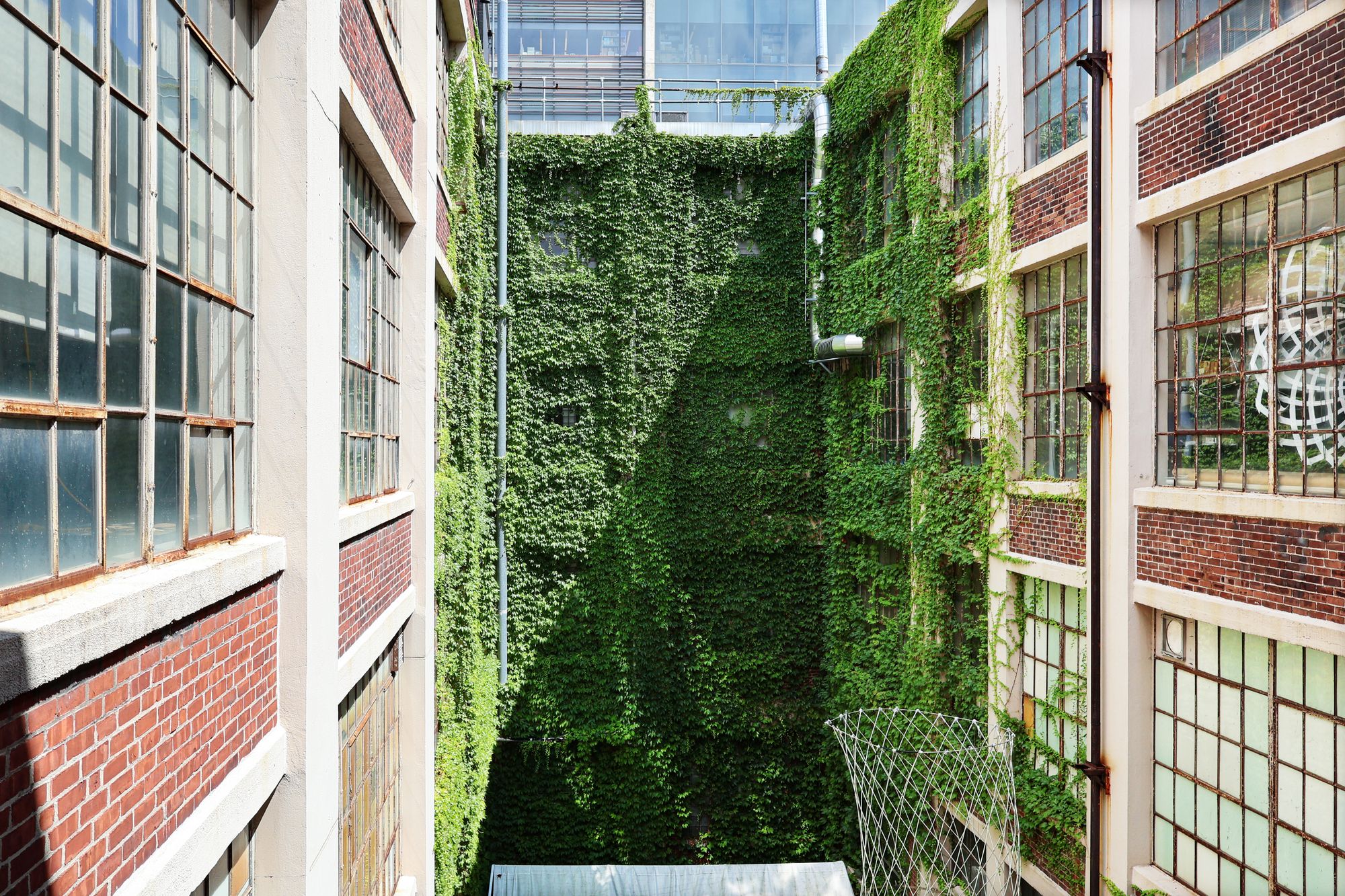
Open Design Studio at MIT
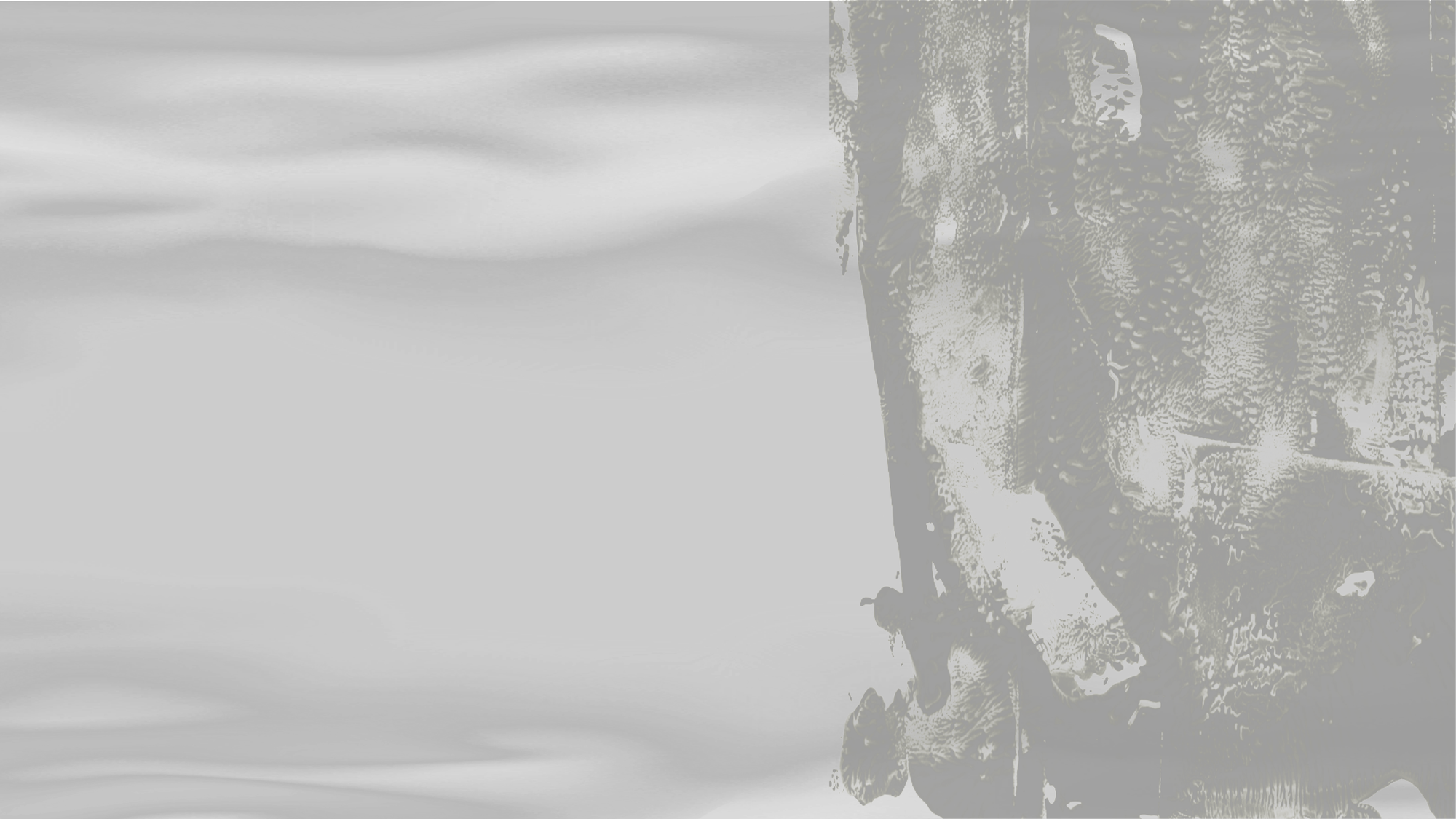
2024 MAD IAP
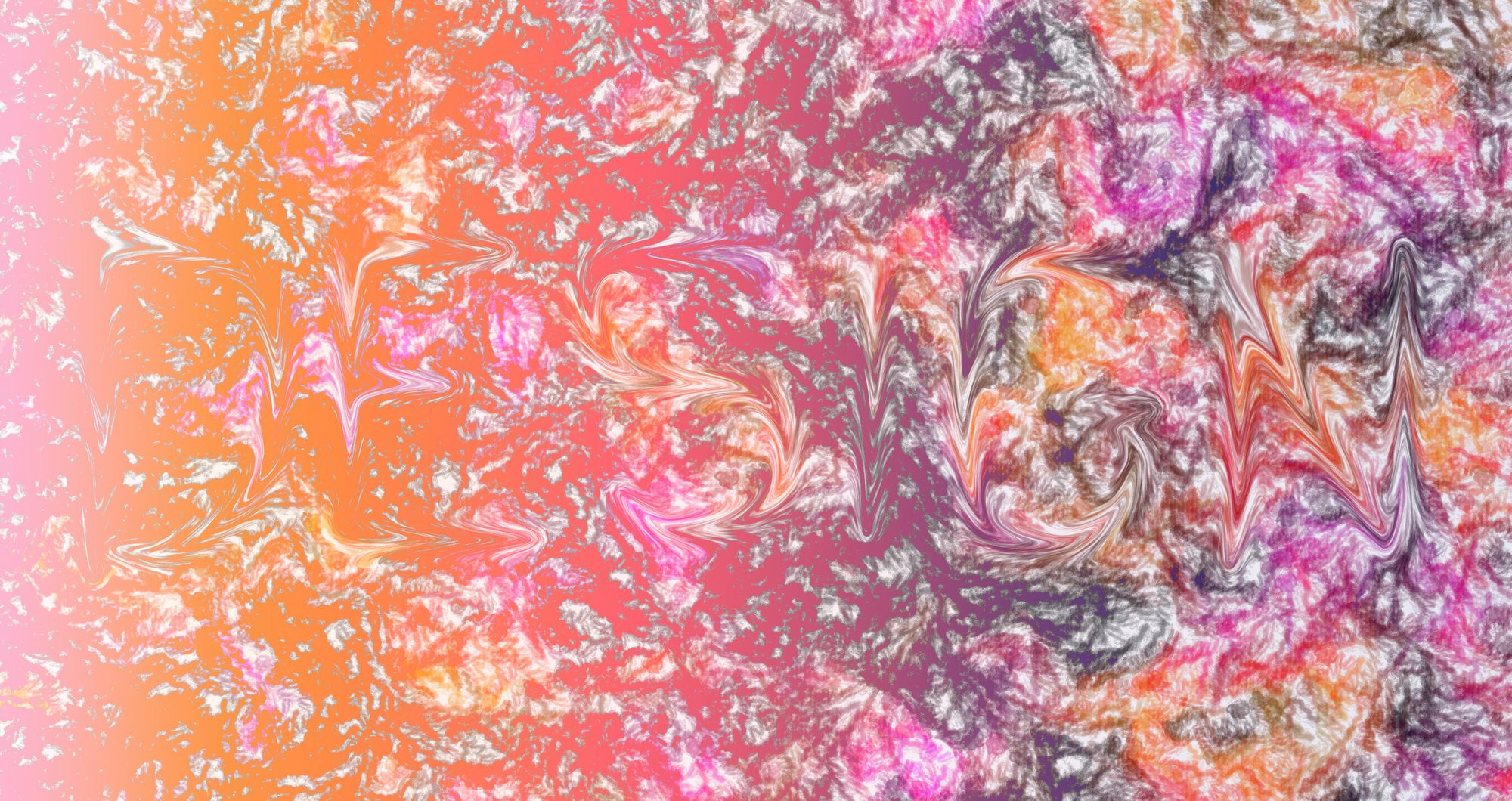