Atacama Biomaterials: A Blueprint for Sustainable Innovation
Atacama Biomaterials is a startup combining architecture, machine learning, and chemical engineering to create eco-friendly materials with multiple applications. Passionate about sustainable innovation, its co-founder Paloma Gonzalez-Rojas highlights how MIT has supported the project through several of its entrepreneurship initiatives, and reflects on the role of design in building a holistic vision for an expanding business.
By Adelaide Zollinger
Dec 15, 2023
Answers by Paloma Gonzalez-Rojas
Q: What is Atacama?
A: Atacama Biomaterials is a venture dedicated to advancing sustainable materials through state-of-the-art technology. With my co-founder Jose Tomas Dominguez, we have been working on developing our technology since 2019. We initially started the company in 2020 under another name and received Sandbox funds the next year. In 2021, we went through the Engines’ accelerator, Blueprint, and changed our name to Atacama Biomaterials in 2022 during the MITdesignX program.
This technology we have developed allows us to create our own data and material library using AI and machine learning, and serves as a platform applicable to various industries horizontally — biofuels, biological drugs, and even mining.
Q: What motivated you to venture into biomaterials and found Atacama?
A: I’m from Chile, a country with a beautiful, rich geography and nature where we can see all the problems stemming from industry, waste management, and pollution.
I care deeply about sustainability, and I have an emotional attachment to stop these problems. Considering that manufacturing accounts for 29% of global carbon emissions, it is clear that sustainability has a role in how we define technology and entrepreneurship, as well as a socio-economic dimension.
When I first came to MIT, it was to develop software in the Department of Architecture’s Design and Computation Group, with MIT Prof. Svafa Grönfeldt as co-advisor and MIT Prof. Regina Barzilay as committee member.
so I reached out to material science and mechanical engineering professors to look into biopolymers and degradable biobased materials. This is how I met my co-founder, as we were both working with MIT Prof. Neil Gershenfeld. Together, we were part of one of the first teams in the world to 3D print wood fibers, which is difficult — it’s slow and expensive — and quickly pivoted to sustainable packaging.
I then won a fellowship from MCSC (MIT Climate & Sustainability Consortium) which gave me freedom to explore further, and I eventually got a postdoc in MIT Chemical Engineering, guided by MIT Prof. Gregory Rutledge, a polymer physicist. This was unexpected in my career path. Winning Nucleate Eco Track 2022 and the MITdesignX Innovation award in 2022, profiled Atacama Biomaterials as one of the rising startups in Boston’s biotechnology and climate-tech scene.
Q: What is your process to develop new biomaterials?
A: My PhD research, coupled with my background in material development and molecular dynamics, sparked the realization that principles I studied simulating pedestrian motion could also apply to molecular engineering. This connection may seem unconventional, but for me, it was a natural progression. Early in my career, I developed an intuition for materials, understanding their mechanics and physics.
It allowed me to optimize a state-of-the-art molecular dynamic software to run twice as fast as more traditional technologies through my algorithm presented at the International Conference of Machine Learning (ICML) this year. This is very important, because this kind of simulation usually takes a week, so narrowing it down to two days has major implications for scientists and industry, in material science, chemical engineering, computer science and related fields. Such work greatly influenced the foundation of Atacama Biomaterials, where we developed our own AI to deploy our materials. In an effort to mitigate the environmental impact of manufacturing, Atacama is targeting a 16.7% reduction in carbon dioxide emissions associated with the manufacturing process of its polymers, through the use of renewable energy.
Another thing is that I was trained as an architect in Chile, and my degree had a design component.
because it allowed me to jump from one technology or discipline to another and understand broader applications on a conceptual level. Our design approach also meant that sustainability came to the center of our work from the very beginning, not just a plus or an added cost.
Q: What was the role of MITdesignX in Atacama’s development?
A: I have known Svafa Grönfeldt, MITdesignX’s faculty director, for almost six years. She was the co-advisor of my PhD, and we had a mentor-mentee relationship. I admire the fact that she created a space for people interested in business and entrepreneurship to grow within the Department of Architecture. She and Executive Director Gilad Rosenzweig gave us fantastic advice and we received significant support from mentors. For example, Daniel Tsai helped us with intellectual property, including a crucial patent for Atacama. And we’re still in touch with the rest of the cohort. I really like this “design your company” approach, which I find quite unique, because it gives us the opportunity to reflect on who we want to be as designers, technologists, and entrepreneurs. Studying user insights also allowed us to understand the broad applicability of our research, and align our vision with market demands, ultimately shaping Atacama into a company with a holistic perspective on sustainable material development.
Q: How does Atacama approach scaling, and what are the immediate next steps for the company?
A: When I think about accomplishing our vision, I feel really inspired by my three-year-old daughter. I want her to experience a world with trees and wildlife when she's a hundred years old, and I hope Atacama will contribute to such a future.
Going back to the designer’s perspective, we designed the whole process holistically, from feedstock to material development, incorporating AI and advanced manufacturing.
Our level of technology-readiness is comparable to the one used by NASA (level 4).
We have proof of concept: a biodegradable and recyclable packaging material which is cost- and energy-efficient as a clean energy enabler in large scale manufacturing. We have received pre-seed funding, and are sustainably scaling by taking advantage of available resources around the world, like repurposing machinery from the paper industry. As presented in the MIT Industrial Liaison and STEX Program recent Sustainability Conference, unlike our competitors, we have cost-parity with current packaging materials, as well as low-energy processes. And we also proved the demand for our products, which was an important milestone. Our next steps involve strategically expanding our manufacturing capabilities and research facilities and we are currently evaluating building a factory in Chile and establishing an R&D lab plus a manufacturing plant in the US.
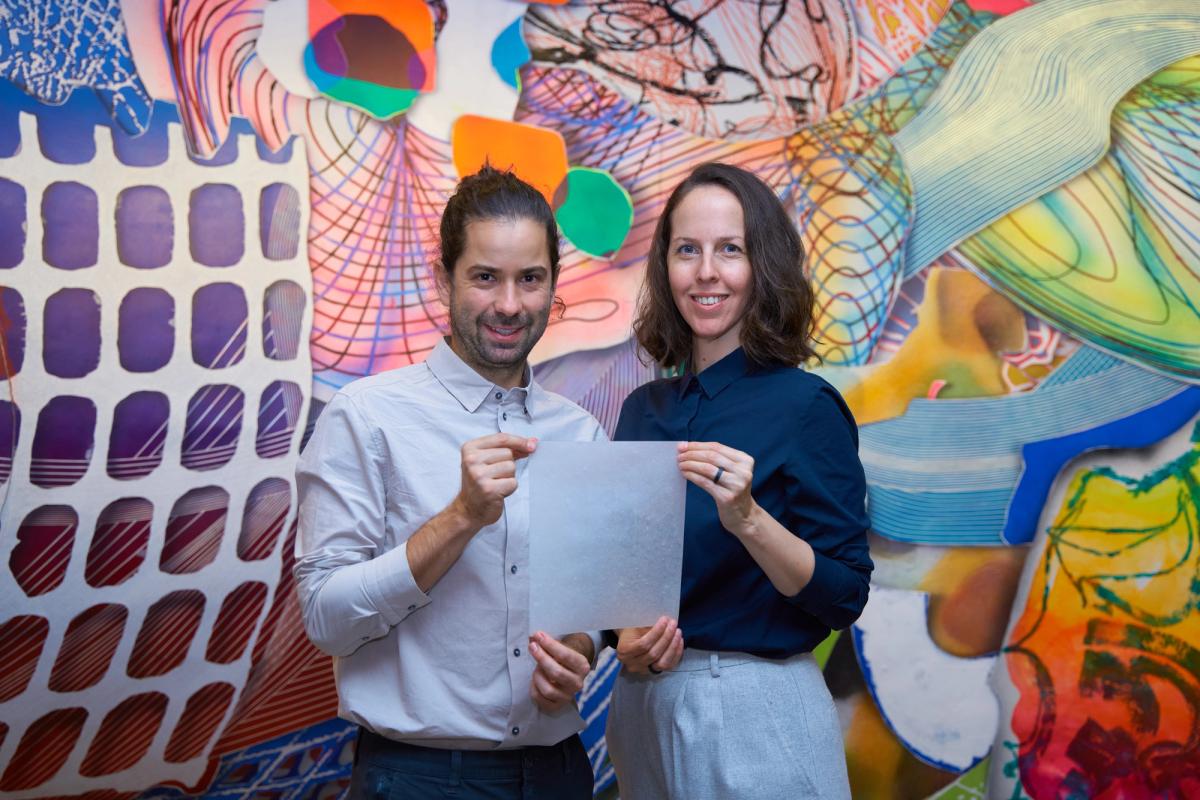
Jose Tomas Dominguez and Paloma Gonzalez-Rojas, both co-founders of Atacama Biomaterials.
Photo: Jade Chongsathapornpong
Related News
Related Events
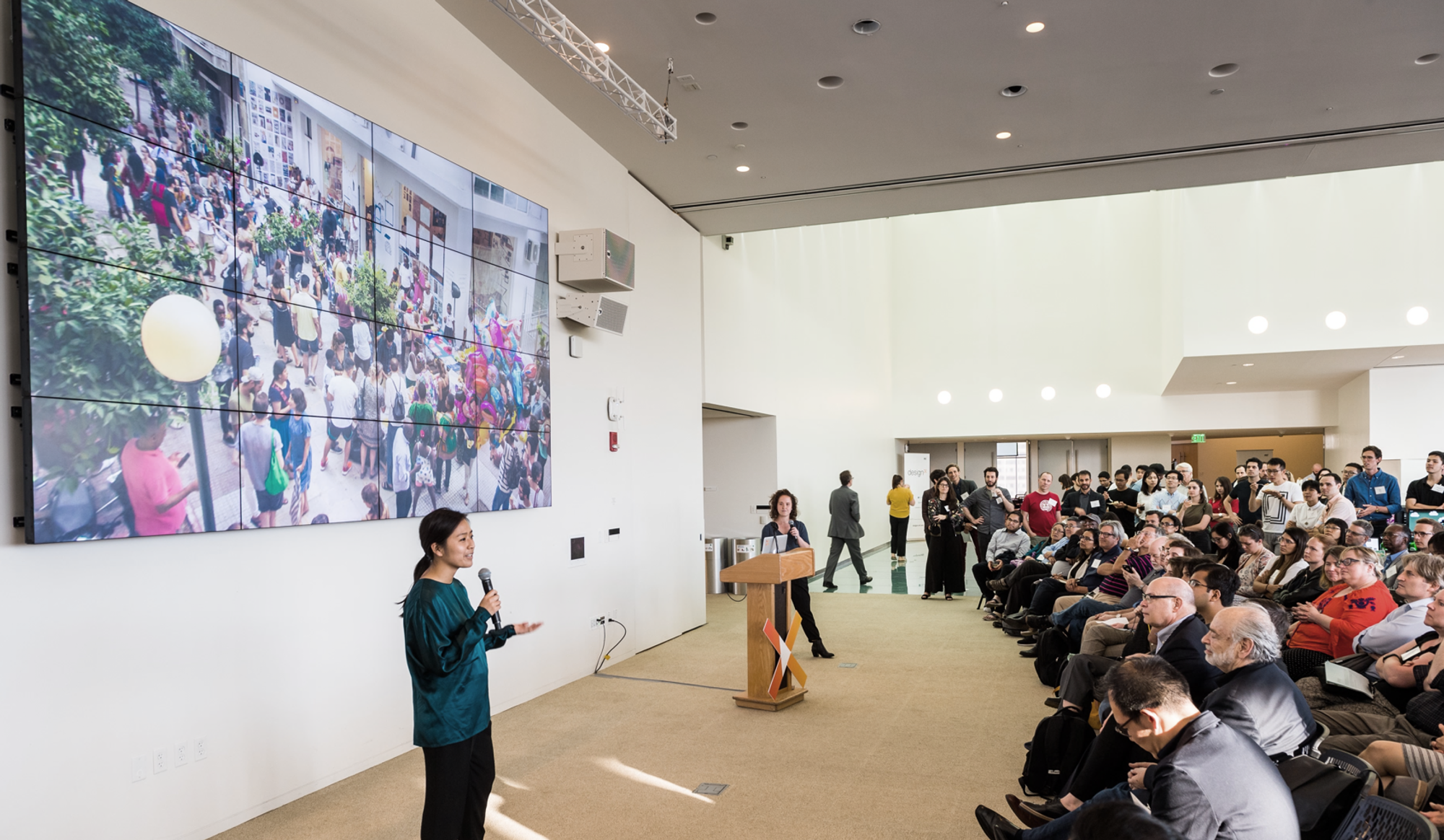
MITdesignX Pitch Day
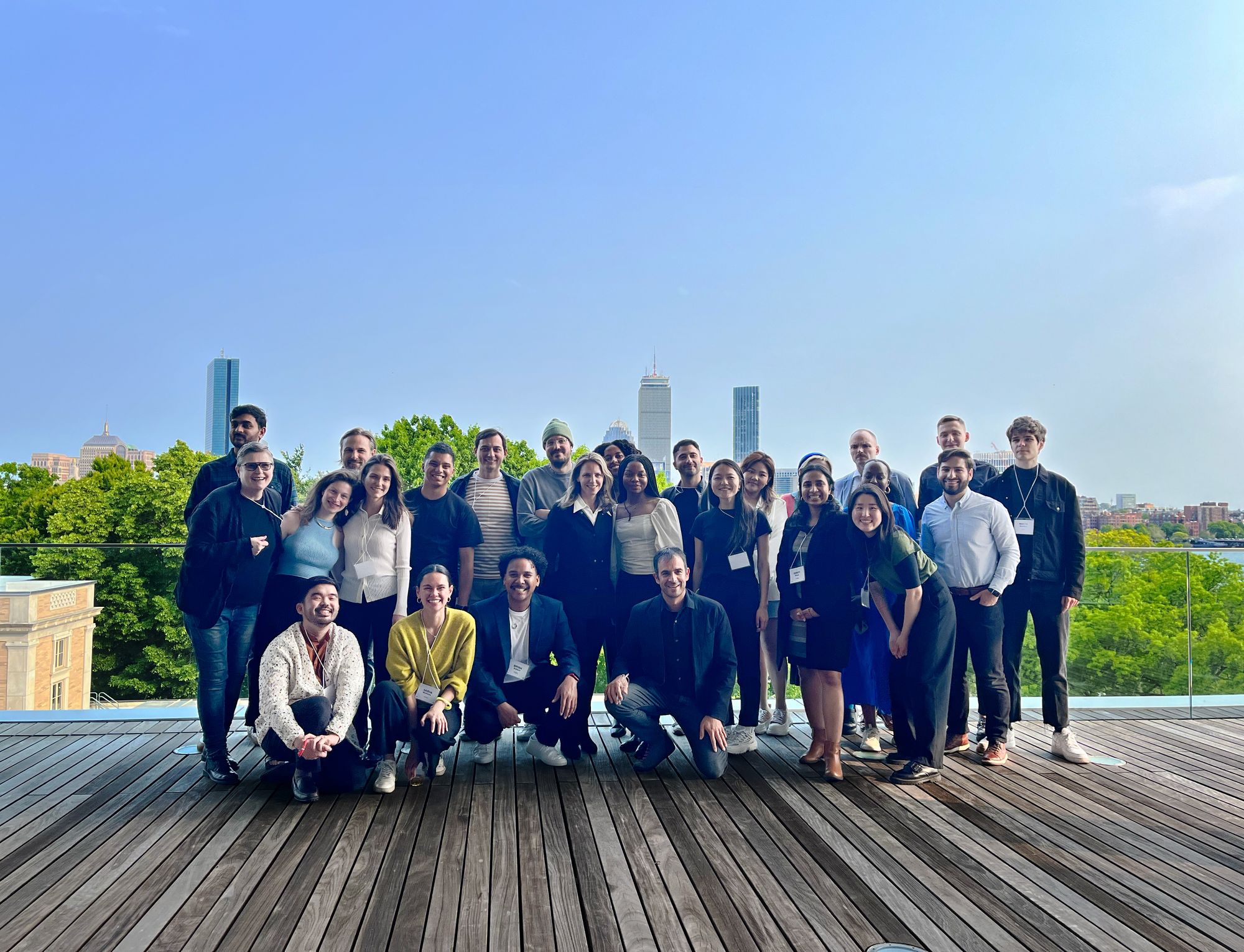